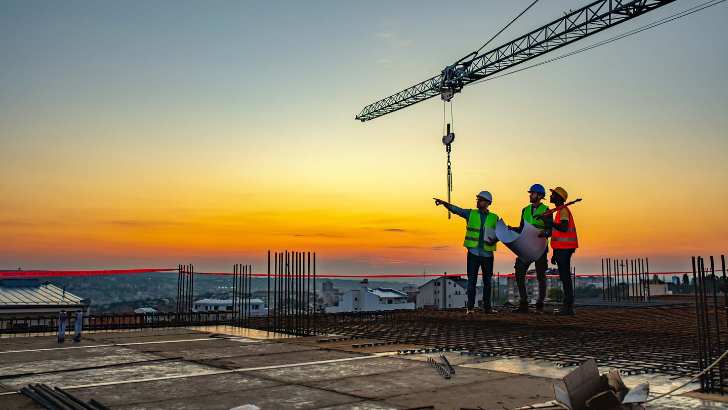
The world is increasingly complex, unpredictable and inter-connected, and being able to manage existing and emerging risks has never been more important. We offer customised risk management and prevention solutions and services for businesses of all shapes and sizes. We can help identify, evaluate and quantify the risks you face, to create a safer more robust business.
Loss Prevention Standards
We have a variety of Loss Prevention Standards to help you protect what matters most to you and your business
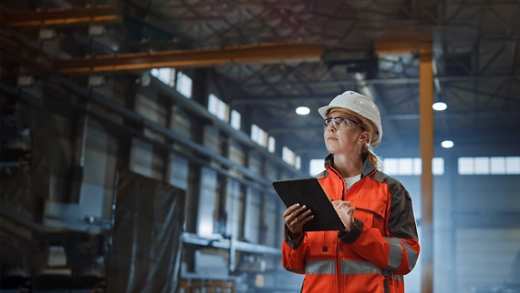
Featured News
What risk management services do we offer?
From physical or virtual surveys to statutory inspections and advice via our helpline, access to our loss prevention standards or specialist partner network, we can help you to protect your business. Want to find out more?
Protecting what matters most
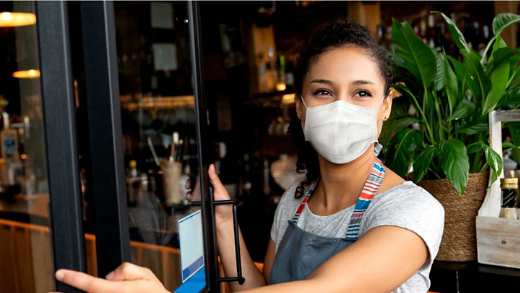
Pandemic Support
Here are some resources to support you through a pandemic.
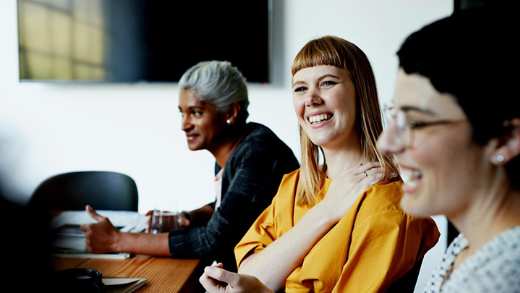
Your People
From your employees to third-party contractors and customers, here’s where to find guidance on key people risks.
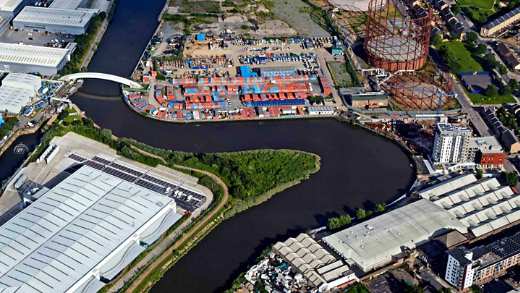
Your Property
From buildings, equipment, and goods to construction projects, here’s where to find guidance on key property risks.
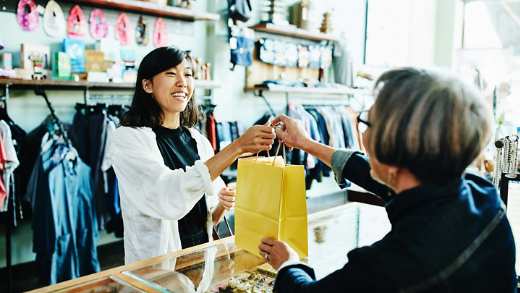
Your Business
From liability to environmental and reputational risks, here’s where to find guidance on how to protect your business.
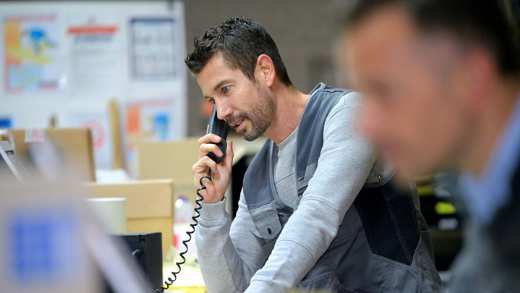
Your Resilience
From planning and supply chains to cyber, business processes and change management, here’s where to find guidance on how to build your resilience.
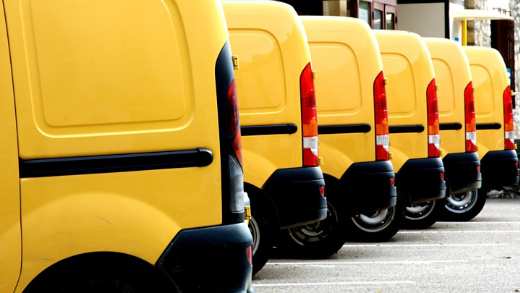
Your Motor Fleet
From your drivers and vehicles to the use of technology and influencing behaviours, here's where to find guidance on managing your motor fleet risks.
Specialist Partners to help minimise your business risks
We've created a network of Specialist Partners to complement our in-house capabilities and to enable our policyholders to benefit from a wide range of risk management solutions at preferential rates and terms. Together, we provide solutions to help with the significant challenges of modern-day risk management.
These partner relationships are wholly for the benefit of our policyholders with no income to Aviva.
To access these services, contact our Specialist Partners.
Resources to better manage your risks
Supply Chain Assessment Tool
Assess your supply chain risk and access advice on how to adopt resilience measures against events that could damage your business.
Aviva Businesslaw
Available to existing Aviva customers at no extra cost. This online service, powered by Farillio, contains a range of regularly updated business and legal guides, document builders, interactive checklists and access to a 24/7 legal advice helpline, to help you achieve your everyday business objectives and manage your exposure to legal risk.
Popular links
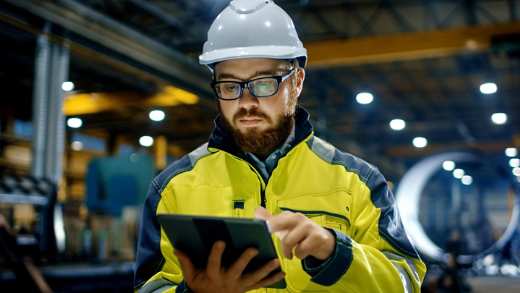
Guidance by Risk Type
Quickly navigate all our guidance here to help manage the relevant risks across your business.
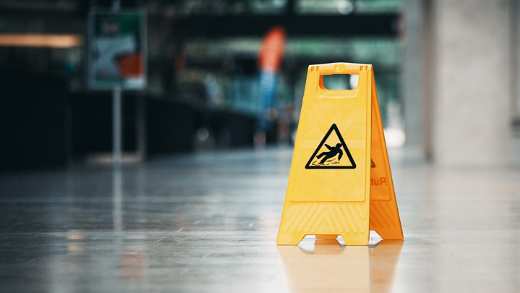
Our Specialist Partner Network
Find out more about the depth of solutions provided by our Specialist Partners.
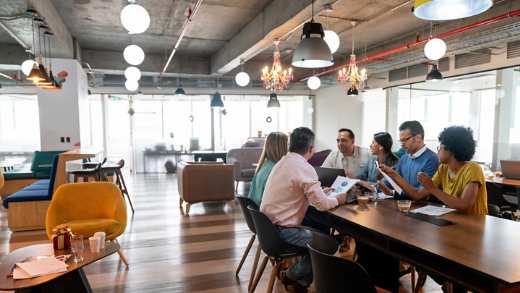
Latest News and Insights
Access all Aviva Risk Management news and insights.
Need further help or assistance?
Call our Risk Help Line to speak to our Risk Management Solutions team for help and advice on
0345 366 6666
Opening times: Monday - Friday* 9:00am - 5:00pm
Email us at: riskadvice@aviva.com
* Excludes Bank Holidays. The cost of calls to 03 prefixed numbers are charged at national call rates (charges may vary dependent on your network provider) and are usually included in inclusive minute plans from landlines and mobiles. For our joint protection telephone calls may be recorded and/or monitored.