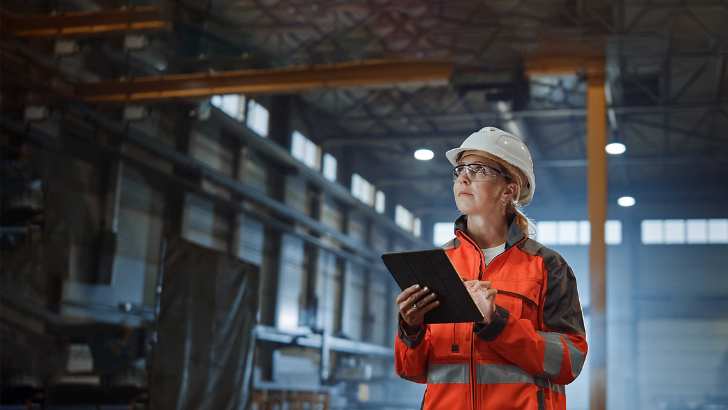
Welcome to our library of risk management guidance which is designed to help you manage risks across your business. You can search the Loss Prevention Standard (LPS) library using key words, or alternatively by navigating the below risk categories.
Your Loss Prevention Standards
Protecting your people
Protecting your property
Protecting you and your business
Building your resilience
Protecting your motor fleet
Need further help or assistance?
Call our Risk Help Line to speak to our Risk Management Solutions team for help and advice on
0345 366 6666
Opening times: Monday - Friday* 9:00am - 5:00pm
Email us at: riskadvice@aviva.com
* Excludes Bank Holidays. The cost of calls to 03 prefixed numbers are charged at national call rates (charges may vary dependent on your network provider) and are usually included in inclusive minute plans from landlines and mobiles. For our joint protection telephone calls may be recorded and/or monitored.